Machine Learning and AI for revolution of Tech Companies are changing and streamlining businesses.
In the ever-evolving landscape of manufacturing, staying ahead of the competition and optimizing processes is vital.
Extended Reality (XR), a revolutionary technology, is paving the way for a transformative shift in the manufacturing industry.
This comprehensive guide is tailored for manufacturing professionals, including engineers, designers, production managers, and C-suite executives.
We will explore Extended Reality Manufacturing Solutions in the industry, along with applications, benefits, development, real-world examples, and best practices for successful implementation.
What is extended reality (XR)?
Extended Reality, commonly referred to as XR, is a broad term that includes various immersive technologies designed to merge the real world with the virtual one.
XR includes Augmented Reality (AR), Virtual Reality (VR), and Mixed Reality (MR).
These digital experience solutions offer distinctive interactions merging physical settings with digital components, presenting users with fresh perspectives and engagement opportunities in their environment.
Augmented reality (AR)
AR enhances the real-world environment by overlaying digital information. For instance, AR can project assembly instructions onto a physical product, aiding workers in the manufacturing process.
Virtual reality (VR)
VR immerses users in a completely digital environment. It is often used for training and simulations, allowing employees to practice complex tasks without real-world consequences.
Mixed reality (MR)
MR combines aspects of both AR and VR, enabling the interaction of digital and physical objects. It is particularly useful for visualizing and inspecting products in real-time.
Why is XR relevant to manufacturing?
Extended reality manufacturing app development has become relevant for several compelling reasons:
XR Benefits in the Industry are spreading widely. With the below-listed XR Benefits for Manufacturers, the industry is growing rapidly by implementing XR.
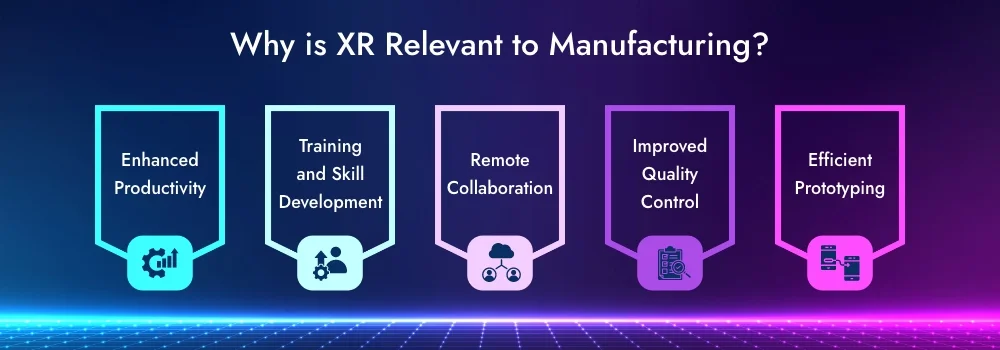
- Enhanced Productivity: XR technologies streamline processes, reduce errors, and enhance productivity on the factory floor.
- Training and Skill Development: XR provides a safe and cost-effective environment for training employees, especially in high-risk industries.
- Remote Collaboration: XR enables experts to provide remote assistance, reducing downtime and minimizing travel costs.
- Improved Quality Control: XR aids in identifying defects, and ensuring products meet stringent quality standards.
- Efficient Prototyping: XR facilitates the rapid development and testing of prototypes, saving time and resources.
XR applications in manufacturing
Extended Reality Manufacturing Solutions is becoming a versatile tool. Some of the applications are as follows:
Product design and prototyping
Manufacturers can create and manipulate 3D prototypes, allowing for more efficient and accurate design iterations.
Virtual training and simulation
XR provides a safe environment for employees to train and simulate complex tasks, reducing the risk of accidents and errors.
Remote inspection and maintenance
Technicians can remotely inspect and maintain complex machinery, reducing downtime and improving maintenance efficiency.
Quality control and assurance
XR technologies help in identifying defects and ensuring products meet the highest quality standards.
Process optimization
Manufacturers can use XR to visualize and optimize production processes, reducing waste and improving efficiency.
Supply chain management
XR assists in tracking inventory and managing the supply chain more efficiently, ensuring products reach customers on time.
Extended reality manufacturing solutions development
Implementing extended reality manufacturing solutions is developing a structured approach:
Identify your needs and goals
Begin by identifying the specific areas in your manufacturing process that can benefit from XR. Set clear goals to measure the success of the implementation.
Choose the right XR technology for your application
Select the most suitable XR technology—AR, VR, or MR—based on the requirements of your application.
Develop or select an XR solution
Depending on the complexity of your needs, you can either develop a custom XR solution or choose from existing ones.
Integrate the XR solution into your manufacturing workflow
Ensure a seamless integration of XR into your existing processes, considering hardware, software, and user interfaces.
Train your employees to use the XR solution
Comprehensive training is crucial for the successful adoption of XR technology. Provide hands-on training to ensure your employees are comfortable with the new tools.
ViitorCloud uses Extended Reality to develop customized solutions according to your requirements.
Extended reality manufacturing solutions examples
Real-world examples of Extended Reality Manufacturing solutions are given below:
- Boeing employs AR glasses to guide workers through the intricate process of assembling aircraft wiring, reducing errors and improving efficiency.
- BMW utilizes VR simulations to train employees in complex production processes, ensuring they are well-prepared for real-world tasks.
- Siemens employs AR technology to guide technicians in maintaining complex machinery, reducing downtime and saving on travel costs.
- Ford utilizes MR to allow workers to visualize and inspect products in real-time, improving quality control and reducing errors.
Best Practices for implementing XR manufacturing solutions
Extended reality manufacturing solutions are transforming the industry. These technologies offer innovative solutions that improve efficiency, safety, and productivity.
ViitorCloud helps in the successful implementation of XR manufacturing solutions which requires careful planning and process to best practices.
Here are some key guidelines for a successful XR integration in manufacturing:
Start small and scale up gradually
Begin with pilot projects in specific areas of your manufacturing process. Once proven successful, expand XR implementation to other areas.
Get buy-in from employees and stakeholders
Involve employees and key stakeholders in the decision-making process to ensure support and enthusiasm for XR adoption.
Provide adequate training
Invest in comprehensive training programs to equip your workforce with the skills needed to effectively use XR technology.
Measure and track results
Continuously monitor the impact of XR in Smart Factories, on your manufacturing processes, and optimize performance.
Conclusion
The future of Extended Reality in manufacturing is promising. XR technologies offer innovative solutions to enhance productivity, improve quality control, and provide cost-effective training.
As manufacturing professionals, embracing XR can revolutionize your operations, keeping you at the forefront of the industry’s evolution.
Develop your projects with extended reality manufacturing solutions, because it’s not just a trend, it is here to stay.
Frequently asked questions
How to implement XR in manufacturing?
Implementing Extended Reality Manufacturing solutions involves defining needs, selecting the right technology, integrating it into workflows, and providing thorough employee training.
How does XR improve manufacturing productivity?
XR improves manufacturing productivity through streamlined processes, reduced errors, and efficient training, leading to enhanced efficiency on the factory floor.
How does XR reduce manufacturing costs?
XR reduces manufacturing costs by minimizing the need for physical prototypes, enabling remote maintenance, and lowering travel expenses through remote collaboration.
How could the manufacturing sector utilize extended reality?
The manufacturing sector can utilize extended reality for product design, training, remote collaboration, quality control, and supply chain management, among other applications.
What are some use cases of XR in manufacturing?
Some use cases of XR in manufacturing include AR-guided assembly, VR-based training simulations, MR-enhanced inspections, and AR-driven quality control.